Ignition
There are three things you need to make an internal combustion gas engine run, ignition, timing and fuel:
So let's talk here about ignition; First the spark:
Spark Plugs:
Most of us do not think much about our spark plugs, in fact I have reached the conclusion after working on cars for the last 35 years that most of you think they should last forever and one plug is pretty much the same as another!
In some ways you are correct and others, well let's just say NO! In today's cars with modern technology and fuel management plugs do seem to last forever, 35,000, 60,000 and even 100,000 miles between changes. But for most of you out there with older vintage cars 15,000 to 25,000 is more like it. There is not a great deal of difference between one top line plug and another beyond your own personal preference ( yes I am ducking now as each of you swears your plug brand is the best) What is different and very important is heat range and tip type - all of those numbers and letters before or after the main number on a plug. Take for instance Champion plug # N12 now this is much different than an N12Y though they will both screw into the same hole. A RBL12Y will not even screw into the same hole. But on the other hand a N12c is totally interchangeable with a N12 but not with a N11. Getting the wrong plug can cause no more problems than fouling out to burning a hole into your piston.
So perhaps we need to revisit that lowly little plug;
picture by Robert Bosch Company
1
: Connector - 2: Shell - 3: Iron/Glass seal - 4: Spark Plug Seat - 5: Insulator Seat - 6: Firing Electrode Pin Cold plugs - Hot Plugs? What does it mean? The ceramic insulator seats on a gasket in the shell, and that is where heat flows out of the insulator into the shell and then into the head of the engine. With more ceramic between the insulator seat and the firing tip heat
travels more slowly away from the tip and the tip stays hotter 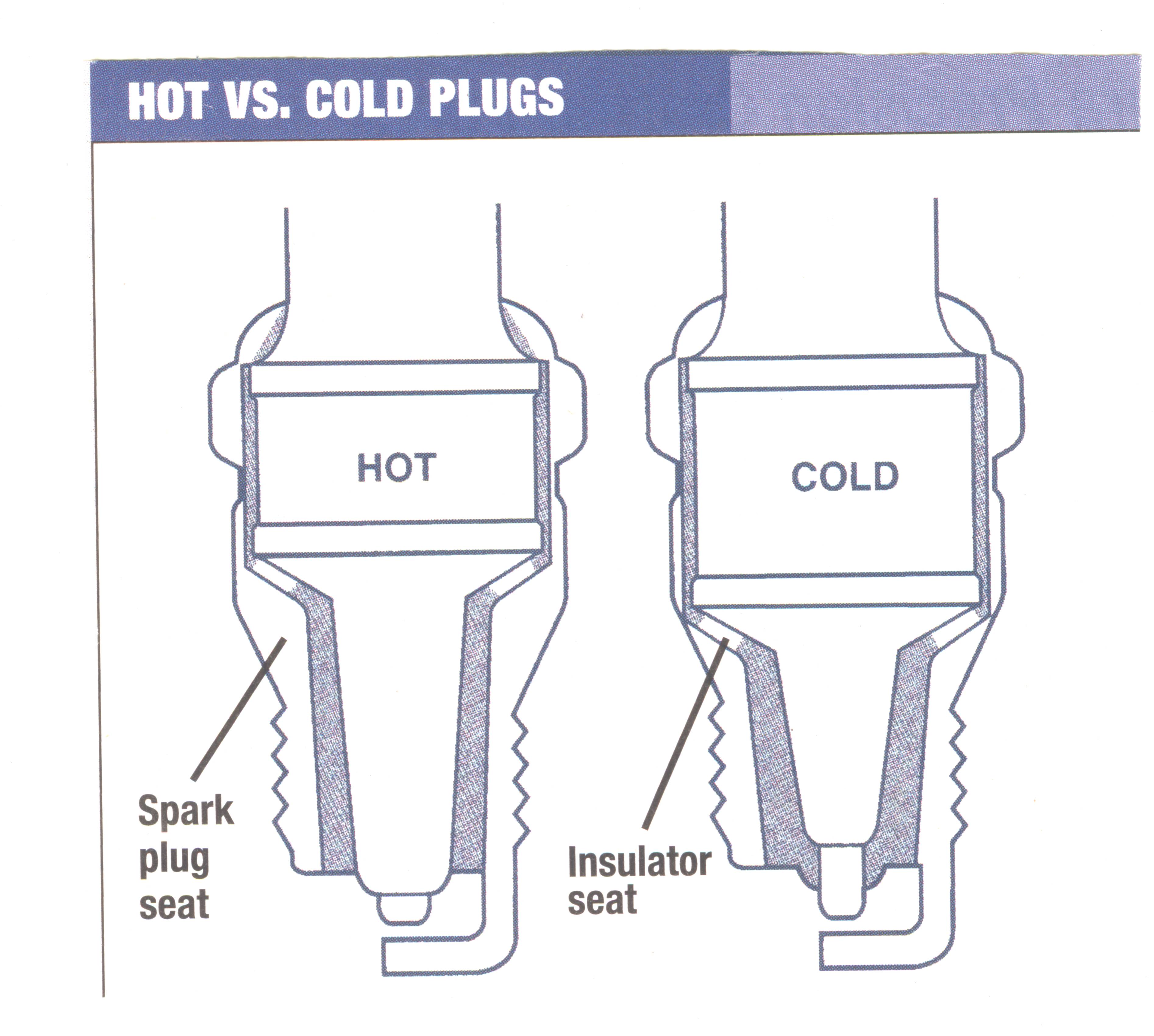
The basic spark plug is much the same as it was 80 years ago. A steel outer shell threaded into the engine provides a ground path, and an insulator with an imbedded center electrode seats in the shell.
The ceramic insulator used in plugs made today is extremely hard, as it needs to withstand very high temperatures, vibrations, insulate high electrical voltages but still conduct heat. Once the insulator is seated in the steel shell, the shell is swaged at the top and then heat shrunk. This is what holds the insulator in place and forms the gas-tight seal that can withstand the pressures created in the combustion chamber. The steel shell is nickel plated to prevent rust and corrosion. You basically have two types of plug seats, tapered or flat. Flat have a compressible gasket and tapered do not. The small peanut plugs used in many late model cars are an example of a tapered seat plug.
Besides just sealing the plug into the combustion chamber the thread and seat transfer heat from the plug. One of the reasons you need clean threads and seat surface in your head. The ground electrode is a separate piece that is welded to the shell. The size, shape and location influence the heat dissipation and spark formation. It is usually made of a nickel-chrome alloy or at least plated with it. Some plugs with special center electrodes may even have a pad of the same material.
The center electrode is where it gets to very interesting. It is actually two pieces. The ignition wire connector and the firing electrode itself. There is actually a slight gap between these two. The connector piece (the part you hook your plug wire to) Is usually copper or nickel-plated copper and extends about two thirds of the way down the insulator. And now is why you buy top line plugs. The most critical part of the plug is where this connector is sealed with a mixture of powdered iron and glass that melts when the shell is heat shrunk. This is the seal that prevent all of the combustion pressure from leaking back up the plug. It also acts as a high resistance conductor between the connector and the firing electrode. This actually increases your firing voltage and is referred to as the iron/glass seal. If you have a radio suppressor plug this is where the suppressor is. The seal also holds the firing electrode in place. The diameter of the firing electrode is smaller than the insulator hole so it can expand without cracking the insulator.
Older plugs center electrodes were made of a nickel-chrome alloy. Latter it was a copper core covered with a nickel-chrome alloy. Remember we need to withstand very high temperatures yet still be conductive. A hardened silver is used in some applications. Though its temperature resistance is less it excels at transferring heat to the insulator and really handles unleaded fuels well. Platinum pads may be mounted at the tip and a matching pad on the ground electrode. This reduces the firing voltage demand greatly. Building a platinum plug gets quite exotic sintered platinum is used and a tiny hole is drilled into the ceramics and then filled with the sintered platinum ( sintered means the powdered metal is heated to become one lump but not heated enough to melt) Platinum will with stand very high temps and higher temps reduce plug fouling and extend the life of the plug and keep good spark formulation.
To keep the tip from developing deposits the plug needs to be above 750 degrees F and it has to get to that temp very quickly after startup. But then you have to be able to shed heat almost as quickly as you build it as the tip can not go over 1650 degrees F even under full load!
Since combustion chamber design and material will play a large role in temperatures and heat transference many types of plugs have been developed to handle this. Extended tips, hot plugs, cold plugs, shielded tips. For most of us the plug recommended by the factory is the correct plug. But, change combustion pressures, increase or decrees fuel flow, change exhaust systems, change cooling systems, all will have a direct effect on the type and temperature of the plug used.
Spark plug gaps are mostly controlled by the capability of the ignition system used. Rule of thumb is a point system can produce or handle no more than 20KV at peak load. And no, putting a coil rated at 40KV will not let you get anymore out of the system. Simple electronic systems, such as many after market bolt on, will produce around 35KV at peak. Hei systems, Chevy is a prime example will produce 50KV at peak. Now plugging a Chevy Hei system into your Triumph and not addressing plug gaps and the like will just give you a system that can produce 50K but will only produce around 19K. The ignition system will only produce enough power to jump the distance between the two electrodes. If I leave my electrodes closed down to the .025 gap that was originally speced the most power it will take to jump that gap is 20KV no matter how much I have in reserve.Ignition
In a previous article we explored the spark plug itself. Let's now look at how the plug gets the power to fire.
For the longest while there was basically one type of ignition system for a gasoline burning engine. Peugeot played around with candles in the late 1800's, but for the most part we can just talk about one system until 1972. The traditional distributor ignition system (DI) used a set of points, a condenser and ignition coil. It was housed in a distributor body that had the ignition wires connected to it through a distributor cap that used an ignition rotor to transfer the electrical pulse generated from the coil to the cap, through the wire, through the plug, back to ground in the cylinder head and hopefully lighting the correct amount of fuel at the correct time.
The system was pretty fail safe and fool proof. Most problems with it came from lack of maintenance. There were some severe limitations as to the amount of power this system could produce but it is still the longest running ignition system in use today.
To work correctly the DI system needs a steady supply of voltage, your battery; A source of high voltage, your ignition coil; A switching device, your points; A way to control the supply voltage to your points, ballast resistor, wire or resisted coil; Something to cut down on the arcing of the points as they open and close, your condenser.
In the DI system the vehicle's system voltage, 13-15 volts running, is reduced to between 6 and 7.5 volts. This is accomplished either pre-ignition coil, through the use of a ballast resistor or resistor wire. You may also have what is called a resisted coil where direct system voltage is applied to the coil and it is reduced internally to the required voltage before heading for the points. One of these ways must be used to reduce voltage or you will burn up your points. A combination of these systems will reduce the voltage supply to the points by to great a factor.
Once we have the proper voltage flowing into and out of our coil we are now ready to convert, or transform (the coil is really nothing more than a transformer) from our low primary voltage to our high secondary voltage. The primary ignition coil winding has a low resistance - typically 1 to 3 ohms - that drops the 6 volt primary supply voltage to approximately zero volts (or as an electrical engineer would say, "consumes all of the voltage") The secondary windings which are 100-200 times the primary windings, transform the current in the primary windings into the secondary windings when the primary switch is opened (your points). Opening the switch (points) cause the magnetic field in the primary side of the coil to collapse and cut across, or fall into, the secondary windings, inducing our secondary current of between 5,000 and 30,000 volts. This is the high voltage that is sent to your plugs.
Not all ignition coils are the same. Each is designed with what is known as a turn ratio, the amount of turns in the primary side windings to the amount of turns in the secondary windings. By changing these ratios a coil can be designed to be better in starting or at peak rpms. Most coils are a balance between the two. As in all in the automotive field to gain one, more power at higher rpm, you lose at another, harder starting.
Some of the drawbacks to a DI system are just the amount of moving parts and connections. Also at best you can only hope for 17,000 to 20,000 miles between point and condenser changes. Plug life is not much better. DI systems typically had a primary resistance of 2.6 ohms. This gave us a coil charge time around 10 ms (milliseconds) While an electronic system typically uses .5 ohm resistance and a charge time around 3.4 ms. What that means is we can produce over 35,000 volts at rpm above 3000! A typical DI system current actually falls off at engine speeds above 1000 rpm. In practical terms this means we have to keep the plug gaps quite small, typically .024 to .028 so the current can jump the electrode to ground and give us our spark to ignite the fuel. Just to get to your plug the current flows from the coil's secondary output, through the coil secondary wire into the distributor cap where it travels through a carbon brush to the ignition rotor. Here it travels along a brass arm and then jumps an air gap to the appropriate electrode in the distributor cap. It then travels down an ignition wire to the spark plug and then jumps from the electrode to ground. Every bit of resistance between the start of the path and the end causes a power loss which means an improper fuel burn is more likely. Anything you do make the path better, clean and tight connections, good parts, will help. Adding big high performance 60,000 volt coils does nothing. The system is incapable of producing that type of current regardless.
As engine temperatures go up and air/fuel mixtures go down (lean) it gets harder and harder to ignite the fuel. Couple that with the fact that as rpm go up in a conventional system we loose ignition power you can understand why older cars used such a rich mixture across the full range of engine demands.
When the federal government began to demand that cars run cleaner the demise of the traditional DI system was a forgone conclusion. When the government mandated 50,000 mile maintenance free ignition systems it was dead. Morn the king, long life to the king. With the advent of the first electronic ignition in 1972 a whole new world in ignition systems was born.
Unless you must use a standard DI system for concurs shows or your vintage racing/rally club demands it I would urge you to switch to some type of electronic ignition system NOW